BASF said it is bundling its carbon management programs to continue its CO2-neutral growth strategy until 2030. To accomplish this, BASF announced continued optimization of its existing processes, gradually replacing fossil fuels with renewable energy sources and developing radically new low-emission production processes.
The company recently presented as examples four projects under this program:
- BASF aims to develop the world’s first electrical heating concept for steam crackers within the next five years. If this energy could come from renewable electricity instead of the natural gas typically used now, CO2 emissions could be dramatically reduced by as much as 90%. Fossil fuels are the largest source of CO2 in the chemical industry according to BASF.
- BASF is developing a new process technology to produce hydrogen from natural gas. This technology splits natural gas directly into its components hydrogen and carbon. The resulting solid carbon can potentially be used in steel or aluminum production, for example. This methane pyrolysis process requires comparatively little energy. The chemical industry uses large quantities of hydrogen as a reactant and producing hydrogen from renewable resources can significantly lower CO2 emissions.
- BASF is looking to develop new low-emission processes especially in the production of high-volume intermediate olefins using new, high-performance catalyst systems. These new-generation catalysts are being marketed in cooperation with Linde. One example is through dry reforming of methane that creates a syngas which is then transformed into olefins via an intermediate step of dimethyl ether.
- BASF is also presenting a new approach for using CO2 as a chemical feedstock: the production of sodium acrylate from ethylene and CO2. Sodium acrylate is an important starting material for superabsorbents, which are widely used in diapers and other hygiene products. BASF experts have made important progress in scaling up this process to industrial scale and have demonstrated that it can be successfully implemented at laboratory scale in a mini plant. Compared to the current propylene-based production method for superabsorbents, in the new process, CO2 would replace around 30% of the fossil fuels.
You can access the webcast research conference on this link.
Editor’s Note:
When it comes to lowering CO2 emissions in chemicals production, it seems BASF is cutting R&D costs by moving away from higher-risks projects such as the use of biotechnology (we know what happened to BASF’s involvement with Synvina). Certainly, recycling CO2 emitted from their current processes and using it as chemical feedstock makes economic sense. I just wonder what will happen to BASF’s ongoing renewable chemicals projects that also reduces CO2 emissions including bio-succinic acid, bio-BDO, and other sugar-based chemicals…
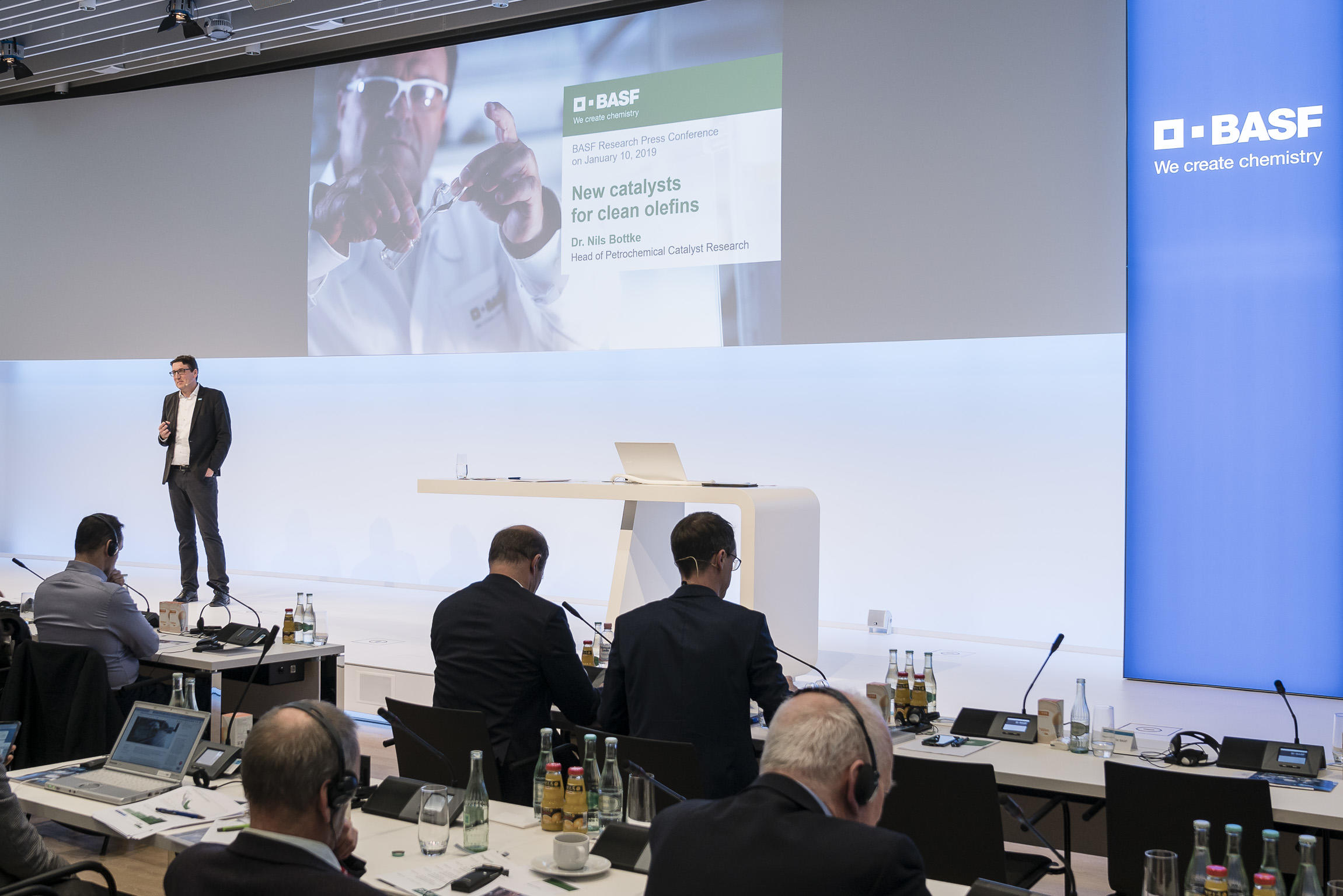